Chinese battery cell manufacturers are gradually rising, but there are still concerns about entering the mainstream supply chain
TIME:2015-08-03 11:05:09
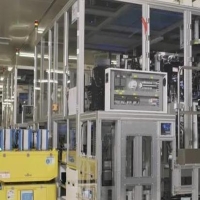
  According to a survey by EnergyTrend, a global market research firm under
TrendForce, Chinese battery cell manufacturers, including new energy and
Guangyu, have gradually emerged, with a more positive capacity expansion rate
compared to Japanese and Korean battery manufacturers. However, the hidden
concerns of Chinese battery manufacturers entering the mainstream supply chain
reveal that the era of low profit in lithium batteries is approaching, and the
gross profit of the lithium battery industry may further explore.   Supply chain diffusion leads to the rise of Chinese batteries   Lithium batteries have been popular in mobile phone products since 2000,
and since 2004, South Korea has been catching up with the production of laptop
batteries. In 2008, due to safety issues with Japanese batteries, it joined the
Chinese battery supply chain, which led to the overall lithium battery supply
chain evolving from being dominated by Japanese brands in the early days to a
situation where Japan, South Korea, and mainland brands dominate.   In terms of the development threshold of lithium batteries, consumer
products such as mobile phones and cameras only require a single battery cell as
their power source due to their small size and low power consumption, and the
battery module assembly process is simple. Overall, cost-effectiveness is the
key to such applications, with the supply chain mainly consisting of three
sources: Japan, South Korea, and China. On the other hand, in laptop products,
due to the high power consumption of the system, multiple series and parallel
battery cells are mostly used to achieve the required voltage and current values
of the system, which raises the safety threshold. Currently, this type of market
is still dominated by Japanese and Korean battery manufacturers.   The huge labor force and rapidly growing domestic demand market in China
have rapidly cultivated the domestic lithium battery industry, covering consumer
and power products from upstream battery materials (Materials), midstream
battery cells (Cells) to downstream battery assembly (Packs).   At present, many important consumer devices choose China as their assembly
base, which has led to many battery cells and battery assemblies also settling
in China. Japanese and Korean battery factories have also established battery
production bases in China, driving the yield improvement of China's battery
industry. At present, with the slowdown in the expansion of polymer battery
production, Chinese battery cell factories are still actively planning for
capacity expansion. In the recent hottest Apple phone supply chain, new Chinese
battery cell factories have also been added. Therefore, whether from the
domestic demand market or the catalysis of their own brands, the potential for
future development of Chinese battery cell factories cannot be
underestimated.   In response to the gradually declining prices of battery cells, battery
cell manufacturers have gradually shifted their business strategies and entered
into battery assembly and processing, including Sony, Samsung, LG, New Energy,
BYD, and others. Especially in square batteries and polymer batteries, they have
fully occupied the supply role of single cell assembly.   According to Energytrend's survey, the current independent assembly and
processing rate of cylindrical battery cell factories has reached over 50%, with
some Japanese factories accounting for more than 70%. Square batteries are
mostly used in mobile phone products, and almost 100% are assembled by battery
cell factories; Due to the high degree of customization in polymer batteries,
the application of a single battery cell is almost entirely independently
assembled by the battery cell factory. Only applications with multiple series
and parallel connections are handed over to the assembly factory for assembly
and processing; Due to the fact that cylindrical batteries are mostly assembled
in multiple series parallel forms, they are mostly assembled and processed by
professional assembly factories.   Regardless of whether it is a single battery cell or multiple series and
parallel applications, battery cell manufacturers, due to their mastery of key
components, sometimes seek assembly orders by lowering the price of battery
cells in order to enter the assembly supply chain. In the long-term development
of supply exceeding demand, the price of battery cells also declines quarter by
quarter. In the long run, the development of gross profit in the production,
manufacturing, and assembly of battery cells is a vicious cycle, It also forces
the relationship between battery cell factories and battery assembly factories
to gradually evolve from the previous upstream and downstream relationship to a
situation of cooperation and competition.   At present, the cylindrical price performance in the third quarter shows a
downward trend in high capacity performance, objectively reflecting an increase
in the proportion of high capacity usage, and the price also shows a reasonable
normal trend of large volume price drops. In the polymer sector, the proportion
of high capacity continues to rise, and many new tablet products that are about
to be launched in the third quarter have abandoned multiple series and parallel
models to increase product appearance features, and have switched to single
larger capacity battery cells for configuration. The main consideration is still
cost, and high capacity battery cells have become more competitive in price,
with a quarterly decline of 3.3%, which is more severe compared to the previous
quarter. The slowdown in the decline in low capacity performance also indicates
a decrease in the proportion of terminal application usage, resulting in a
slight decline in the price trend of battery cells.